Formel ½ für Maschinenbauer
Die MAG-IAS GmbH wird die Konstruktionszeit für die kompletten Bearbeitungslinien von Kfz-Motoren um mehr als die Hälfte verkürzen. Möglich wird das durch den Umstieg auf die mechatronische Konfiguration mit einem gewerkeübergreifenden, funktionalen Baukasten.
Die MAG-IAS GmbH wird die Konstruktionszeit für die kompletten Bearbeitungslinien von Kfz-Motoren um mehr als die Hälfte verkürzen. Möglich wird das durch den Umstieg auf die mechatronische Konfiguration mit einem gewerkeübergreifenden, funktionalen Baukasten. Die Voraussetzung dafür schafft das EPLAN Engineering Center (EEC). Es sorgt dafür, dass in der Konstruktion des weltweit agierenden Unternehmens Kapazität für kreative Ideen und für das geplante Wachstum geschaffen wird. Wenn ein Automobilhersteller die Fertigung eines neuen Motors plant, ist die Wahrscheinlichkeit hoch, dass er Kontakt zu MAG-IAS aufnimmt. Denn das in Eislingen bei Stuttgart ansässige Unternehmen gehört zu den wenigen weltweiten Spezialisten, die komplette Fertigungslinien für die vollautomatisierte Produktion von Motorblöcken, Zylinderköpfen und Kurbelwellen projektieren und fertigen
Komplette Fertigungsanlagen mit z.T. über 100 Maschinen
Diese Produktionsanlagen bestehen aus vielen Einzelmaschinen, meist Bearbeitungszentren aus der „SPECHT“-Serie von MAG, die jeweils einzelne Bearbeitungsschritte wie z.B. Drehen, Fräsen oder Honen übernehmen und dabei mit bis zu 16 Achsen sehr flexibel sind. Dafür sorgt ein Baukastensystem, das eine vielfältige Anpassung der Maschine an die jeweilige Aufgabe erlaubt. Dieser Baukasten war allerdings ursprünglich nur auf der mechanischen Ebene angelegt, und seine Grundlage bildeten physische Baugruppen und Bauteile wie Ständer, Spindeln und Werkzeugwechsler. Als Dipl.-Inf. Werner Binsmaier vor drei Jahren als Leiter Elektrik und Software in das Unternehmen eintrat, hatte er u.a. das Ziel, die Potenziale der automatisierten Konstruktion nutzbar zu machen, und erhielt dafür die Rückendeckung des Vorstandes. Das Unternehmen hatte erkannt, dass es zwar mit dem rein mechanischen Baukasten in der mechanischen Konstruktion Einsparungen erzielte, die Engineering-Zeiten in den Disziplinen Elektrik, Fluidik und Software aber eher anstiegen, weil der mechanische Baukasten einen größeren Konfigurationsraum ermöglichte und so die Anforderungen und Bedürfnisse der Steuerungstechnik größer wurden. Das Anforderungsprofil war somit klar definiert: Gewünscht war ein disziplinübergreifender mechatronischer Konstruktionsbaukasten, der sich klar und eindeutig nach Funktionen strukturieren lässt. Die Software sollte sich an die Arbeitsabläufe von MAG anpassen lassen und auch mit der vorhandenen Vertriebssoftware harmonieren, die das Unternehmen für die Projektierung und Kalkulation nutzt.
Entscheidung für das EEC
Ein solches System hatte Werner Binsmaier mit dem EEC bereits kennengelernt, und weitere Marktrecherchen sowie Gespräche mit Experten aus der Wissenschaft und Praxis bestärkten die Verantwortlichen bei MAG in der Entscheidung für das EEC. Die Implementierung wurde sehr systematisch und strukturiert vorangetrieben. Werner Binsmaier: „Wir haben ein Team von je einem Konstrukteur aus den beteiligten Disziplinen Mechanik, Elektrotechnik, Fluidik und Software-Entwicklung gebildet, dessen Hauptaufgabe die Strukturierung des mechatronischen Baukastens und die Definition der erforderlichen Schnittstellen ist.“
Schritt für Schritt zum mechatronischen Baukasten
Mit dieser Aufgabe ist man inzwischen gut vorangekommen: „Die Elektrotechnik-Entwicklung nutzt den Baukasten bereits mit EPLAN Electric P8 als Zielsystem. Zurzeit werden die Fluidtechnik und die Software-Entwickler an das EEC angedockt, die Mechanik und die Dokumentation folgen später.“ Das Ziel, das MAG-IAS dabei verfolgt, ist klar definiert: „Unsere Wunschvorstellung ist ein disziplinübergreifender Baukasten, der aus reinen Funktionen besteht und jeder Funktion die dazugehörigen Bauteile mit ihren Leistungsdaten und Abmessungen zuordnet.“
Andere Sichtweise auf die Engineering-Projekte
Den Verantwortlichen ist klar, dass das EEC die Sichtweise auf den Konstruktionsprozess ändert, und eben das ist gewünscht: „Wir wollen in Funktionalitäten denken statt in Bauteilen, Stücklisten und Gewerken. Für eine solche mechatronische Sichtweise brauchen wir ein starkes Tool, das sozusagen als ´Leitplanke´ dient und das haben wir mit dem EEC gefunden“, so Werner Binsmaier. Wobei dem Tool auch klare Grenzen gesetzt sind: „Es geht hier immer um das operative Projektgeschäft, d.h. um die Auswahl und Konfiguration von Maschinenvarianten und nicht um die Entwicklung gänzlich neuer Maschinentypen. Hierfür haben aber die Ingenieure zukünftig wieder mehr Zeit zur Verfügung."
Ergebnis: Zeitersparnis von mehr als 50 %
Welche konkreten Ergebnisse sehen die MAG-Entwickler nach der Einführung des EPLAN Engineering Centers? Die Elektroingenieure konnten die Konstruktionszeit bereits anfänglich um rund 40 % verkürzen und können mit Einführung des EEC in den weiteren Konstruktionsdisziplinen bis zu 60 % Verkürzung in der Elektrik erreichen. Werner Binsmaier: „Das entspricht recht genau den zuvor errechneten Einsparungen, auch wenn es etwas länger gedauert hat, dieses Ziel zu erreichen. Für die Fluidik, die mit Hydraulik, Pneumatik, Kühlung und Schmierung gleich vier Mediensysteme entwickelt und mit EPLAN Fluid arbeitet, wird mit Einsparungen in gleicher Größenordnung gerechnet. „Für die Software rechnen wir mit ebenfalls mehr als 50 % kürzeren Entwicklungszeiten, weil die Module nach Elektrik und Fluid noch stärker standardisierbar sind und wir so einen wesentlich robusteren Softwarebaukasten in EEC abbilden können. Hinzu kommt der Aufwand für die Pflege des Baukastens, den wir pro Gewerk auf 20 % schätzen – anfangs mehr, später aber deutlich weniger.“ Die Verkürzung der Entwicklungszeit ist für MAG ein kaum zu unterschätzender Vorteil, weil die Projektlaufzeiten immer kürzer werden. Wenn der festgesetzte Abnahmetermin nicht eingehalten wird, sind die Strafen empfindlich. Der Zeitvorteil hat aber auch noch einen anderen positiven Effekt: Die Anlagen lassen sich im Auftragsstadium besser kalkulieren und die Planungssicherheit wird deutlich gesteigert. Außerdem können die Entwickler ihre Arbeit später im Projektverlauf starten, wenn schon größere Planungsumfänge festgezurrt sind. Umso geringer ist dann die Wahrscheinlichkeit, dass es später zu Änderungen kommt.
Empfehlung: Gut planen, umfassend umsetzen
Welche Empfehlungen gibt Werner Binsmaier anderen Maschinenbauern, die ihre Konstruktionssystematik in Richtung Mechatronik trimmen möchten? „Ein solcher Schritt ist eine große Chance, die man so umfassend wie möglich nutzen sollte – nach dem Motto ´Ganz oder gar nicht.´ Wir hatten deshalb für mehrere Monate einen EPLAN Consultant im Haus und haben uns viele Gedanken über die Optimierung und Strukturierung der Prozesse gemacht. Aus unserer Sicht hat sich dieser Aufwand gelohnt. Wir arbeiten jetzt mit einer deutlich besseren Methodik, konnten die Konstruktionszeit um mehr als die Hälfte reduzieren, sind agiler im Prozess, können schneller auf Änderungen von Seiten des Kunden reagieren und werden das mechatronische Konfigurieren mit dem EEC desto besser nutzen, je mehr Disziplinen wir in den Prozess integrieren.“
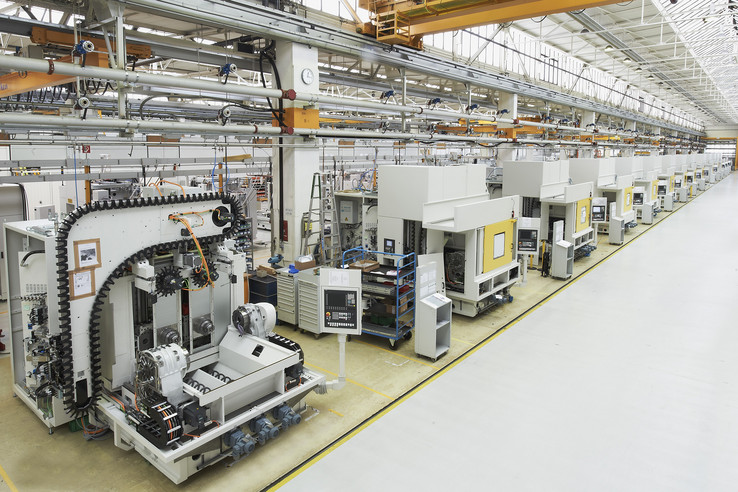
Basis der kompletten MAG-Fertigungslinien ist die SPECHT-Baureihe, zu der Dreh- und Fräsmaschinen sowie Bearbeitungszentren mit einer oder zwei Spindeln gehören.
Bild: MAG-IAS GmbH