Am „Sweet Spot“ der Elektromobilität
Voltabox treibt den Trend Elektromobilität maßgeblich voran
Welche Batterie-Applikationen sind auf dem Weg in den Massenmarkt? Batterien für die stationäre Energiespeicherung, industrielle Großbatterien oder Lösungen speziell für die Elektromobilität? Wie viele Kilowattstunden lassen sich in welchem Bauraum und bei welchem Gewicht speichern? Wie ist es um Ladezeit und Lebensdauer der Batterie bestellt? Wenn selbst Tageszeitungen solche Fragen aufgreifen, ist klar: Die Batterie-Branche zählt zu den innovativsten Industriesegmenten weltweit.
Im Zentrum einer breit geführten Diskussion agiert die auf die Entwicklung und Fertigung moderner Lithium-Ionen-Batteriesysteme spezialisierte Voltabox AG aus dem westfälischen Delbrück. Damit das Batteriesystem als Schlüsselkomponente einer neuen Ära in Leistung und Preis überzeugen kann, schöpft Voltabox bei der Batterieentwicklung das Automatisierungspotenzial im Kabel- und Kabelbaumdesign mit EPLAN Harness proD voll aus. Christopher Bern, Teamleiter Batterie-Systementwicklung bei Voltabox, sagt: „Wir haben festgestellt, dass kein anderes Tool so schnell zu erlernen und intuitiv zu bedienen ist wie Harness – auch bietet die Verbindung zwischen Electric P8 und Harness so viele Vorteile, dass wir darauf nicht verzichten wollen.“
In der Mitte der Wertschöpfungskette
Voltabox sieht sich am „Sweet Spot“ der Elektromobilität angesiedelt – also mit seinen Batteriesystemen genau in der Mitte der Wertschöpfungskette. Das Unternehmen verfügt über drei Geschäftsbereiche. Der Geschäftsbereich Voltapower bietet kundenspezifische Batteriesysteme für industrielle Anwendungen. Diese kommen zum Beispiel in Gabelstaplern, Bergbaufahrzeugen, Oberleitungsbussen und fahrerlosen Transportsystemen zum Einsatz. Ein weiteres Geschäftsfeld bildet Voltaforce, das sich auf Lithium-Ionen-Batterien für den Massenmarkt spezialisiert hat. Der Schwerpunkt liegt auf Starterbatterien für Motorräder und Sportwagen sowie Batteriepacks für Pedelecs und E-Bikes.
Hinzu kommt der Geschäftsbereich Voltamotion, der sich auf die Entwicklung von elektrischen Antriebssystemen konzentriert, also Komponenten, die zur Elektrifizierung von Antriebssträngen benötigt werden. Am firmeneigenen Forschungszentrum in Aachen werden solche Antriebskomponenten entwickelt, wie beispielsweise die Leistungselektronik zur vollständigen Elektrifizierung von Hochleistungsfahrzeugen samt hocheffizienten Elektromotoren.
Spannung garantiert – Batterieentwicklung
Christopher Bern spricht durchaus Klartext, wenn es um das kernige Spannungsfeld geht, in dem sich die Voltabox-Konstrukteure befinden: „Es gilt, kundenspezifische Lösungen in kürzester Zeit zu entwickeln. Erste Prototypen sollen bereits seriennahen Stand aufweisen.“ Auch müssten Prototypen und Kleinserien schon kosteneffizient realisiert werden oder Anpassungen jederzeit schnell und unkompliziert umzusetzen sein. Das ist kein Kann, sondern ein Muss, wenn man in einer der dynamischsten Branchen weltweit ganz vorn mitspielt: „Wir stellen höchste Qualitätsansprüche an uns selbst und unsere Premiumprodukte, da ist es eine logische Schlussfolgerung, wenn hier zwei Marktführer zusammenarbeiten.“ Der eine ist Voltabox, der andere EPLAN. Mit EPLAN Electric P8 für die Elektroprojektierung und EPLAN Harness ProD fürs Kabel- und Kabelbaumdesign in 2D und 3D Lösungen werden die Automatismen und Kollaboration im Workflow erst ermöglicht. Der Blick in den Batterieentwicklungsprozess bei Voltabox beleuchtet das Wie und Warum.
Voltabox‘ Entwicklungsprozess
Vier Arbeitsschritte lassen sich im Batterieentwicklungsprozess skizzieren: die 3D-Bauraumuntersuchung und der Schaltplanentwurf, die Komponentenplatzierung und 3D-Kabelbaumentwicklung, die Prototypenfertigung und Konfektionär-Anfragen sowie die Dokumentation. Voltabox will schnell erstklassige Ergebnisse erzielen – das ist mit einem sequenziellen Workflow isolierter Abteilungen und Insellösungen nicht zu machen. Während der Voltabox-Kunde Angaben zu Bauraum und mechanischen Konstruktionsdaten der Zielapplikation macht, wird parallel bereits das Schaltungskonzept entworfen. Beide Datenpakete werden in EPLAN Harness proD importiert, „dann kann die Komponentenplatzierung schon beginnen“, so Christopher Bern: „Leitungswege werden definiert und entsprechend des Schaltplans vernetzt, nach und nach entstehen einzelne Baugruppen.“ Die äußere Verkabelung eines Batteriesystems umfasst häufig, neben der Hochvoltverkabelung von mehreren Batteriecontainern, die Kommunikation mit dem Zentralen Steuergerät, das einen jederzeit sicheren Batteriebetrieb gewährleistet und die Schnittstelle zwischen Batterie und Fahrzeug darstellt.
Die generierten Baugruppen lassen sich exportieren und an die mechanische Konstruktion zurückspielen, um entsprechende Änderungen und Entwicklungsschleifen zu berücksichtigen. Das ist insofern einfach, als EPLAN Harness proD offen zu MCAD-Systemen ist und entsprechend einfach in bestehende Systemlandschaften integriert werden kann. Der Prototypenbau, dem mit dem Leitungssatz, der Stückliste aller benötigten Komponenten und der Oberflächenschutztabelle etc. alle notwendigen Informationen aus EPLAN Harness proD vorliegen, fertigt im Anschluss erste Muster; parallel entstehen Ableitungen von Kabelzeichnungen und Nagelbrettern, um die Konfektionär-Anfragen zu starten. Automatisch leitet EPLAN Harness proD die Dokumentation inklusive Nagelbrett und Kabelzeichnung ab: „Betriebsanleitungen, Aufbaudokumentationen für die Fertigung und Visualisierungen – für alle schnell verständlich – sind unerlässlich“, so Christopher Bern, „ein solches System hat ja anfangs noch gar nicht existiert.“
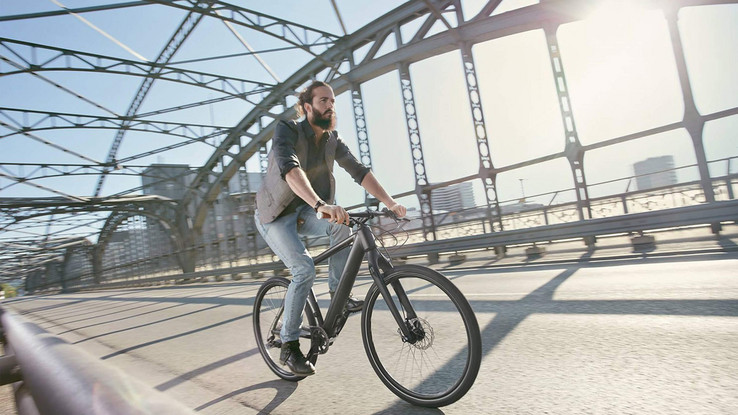
Kundenspezifische Batteriesysteme kommen beispielsweise bei E-Bikes und Pedelecs zum Einsatz.
Bild: Voltabox AG
Das Point & Klick-Prinzip greift
Die Anforderungsanalyse durch die Voltabox AG führt zunächst auf die Auswahl der idealen Batteriezelle, für die eine passende Verschaltung von entsprechenden Modulen entworfen wird. Das Systemkonzept wird zusammen mit der mechanischen Konstruktion entwickelt und anhand der Daten zur Zielapplikation überprüft. Christopher Bern: „Hier geht es um den verfügbaren Bauraum, also auch darum, ob das Handling-Konzept passt oder die Befestigungen zugänglich sind.“ Die Auswahl und Platzierung von Teilkomponenten und Leitungen erfolgt über die Harness Library, die Voltabox als Komponentendatenbank selbst aufgebaut hat, und die auch Zubehörteile wie Blindstopfen oder Kammerdichtungen umfasst. „Wir können mit nur wenigen Klicks alles im Bauraum platzieren, die Verschaltung des Last- und Kommunikationsteils ist sehr schnell realisiert“, so Bern, der nicht nur den Austausch mit der Mechanik, sondern auch das Zusammenspiel von Elektroprojektierung und Kabelbaumdesign explizit anspricht: „Die Harness-Schnittstelle zu Electric P8 ist ein Riesenvorteil und erleichtert das Leben des Entwicklers ungemein. Wir können automatisiert Vernetzungspläne übernehmen.“
Wirklich effizient lasse sich zudem auch die Ableitung der Baugruppen-Zeichnungen gestalten, wobei Änderungen automatisch übernommen, also aktualisiert, und mit Informationen angereichert werden. Stichwort Austausch: Die umfangreiche Export-Schnittstelle zwischen MCAD und ECAD sorgt für schnellere Entwicklungsschleifen bei der Entstehung des digitalen Batteriesystem-Zwillings. Die mechanische Konstruktion kann Leitungssätze und platzierte Komponenten wieder in ihr System einspielen und entsprechende Anpassungen, wie Befestigungen und Durchbrüche, vornehmen, um Leitungssätze sicher ins Batteriesystem zu implementieren.
Die Zusammenarbeit zwischen den einzelnen Bereichen in der Entwicklung steht im Mittelpunkt eines effizienten Entwicklungsprozesses. Dabei erreicht Voltabox eine neue Stufe der Integration mit der anstehenden Anbindung von EPLAN Harness proD ans PDM-System, die mit der EPLAN ERP/PDM Integration Suite umgesetzt wird.
Digitaler Zwilling: Zukunft im Blick
Vorher wissen, wie das System nachher funktioniert. Das ist mit EPLAN Harness proD realisierbar und gefällt jedem Konstrukteur: „Es ist eindrucksvoll zu sehen, wie nahe das reale System dem zuvor entworfenen digitalen Zwilling kommt“, sagt Christopher Bern und verweist auf die Vorteile der faktisch simulierten Batteriesystemprüfung auf dem Schreibtisch anhand des digitalen Zwillings: „Wir können mit Harness alles im Vorfeld prüfen und Fehler frühzeitig aufdecken, und zwar ohne den Aufbau erster Prototypen: Montierbarkeit, Leitungswege in Bezug auf den Platz in der Zielapplikation oder die Erreichbarkeit von Steckverbindungen. 90 % der Aufgaben sind damit bereits in 3D lösbar und die Prototypen-Aufwände auf ein Minimum reduziert.“
Dass mit EPLAN Harness proD auch die Leitungswege ohne Prototypen definiert werden können und die Stücklisten für die Fertigung automatisch erstellt werden, forciert den Workflow ebenso wie der verzahnte Änderungsprozess: „Ein Beispiel: Wir wollen einen einzelnen Pin am Steuergerät wechseln und müssen uns eben keine Gedanken machen, ob in allen Zeichnungen und Ableitungen dieser Wechsel auch übernommen wurde: Das Tool denkt automatisch mit, weist drauf hin, ändert mit.“ Komplett automatisiert läuft die Leitungsvermessung in EPLAN Harness proD. „Das ist ein sehr wichtiger Punkt“, so Christopher Bern, „wenn auch im ersten Moment gar nicht so präsent. In der konventionellen Leitungsentwicklung werden erste Muster aufgebaut und auf Tauglichkeit überprüft, der Leitungssatz wird händisch vermessen und entsprechende Zeichnungen und Nagelbretter entworfen. Das passiert hier mit wenigen Mausklicks.“
Klar ist: keine Anwendung ohne einen Exoten. Da macht Voltabox beim Einsatz von EPLAN Harness proD keine Ausnahme: „Was bei uns intern gern gemacht wird: die Verschlauchungen auch in EPLAN Harness zu realisieren. Wir legen einfach einen Leitungssatz der entsprechenden Eigenschaften des zu verwendenden Schlauches an, fertig.“
Autor: Ulrich Kläsener, freier Redakteur, Bergisch-Gladbach
Voltabox AG
Mit ihren sicheren und wirtschaftlichen Lithium-Ionen-Batteriesystemen gilt die Voltabox AG als Wegbereiter für nachhaltige Mobilität. Rund 275 Mitarbeiter – darunter 81 in Forschung und Entwicklung – erwirtschafteten 2018 einen Umsatz von rund 67 Mio. Euro. Für 2019 wird ein Umsatz von 105 bis 115 Mio. Euro durch eine ausgeweitete Geschäftstätigkeit im nordamerikanischen und europäischen Intralogistik-Geschäft sowie bei Batterien für Pedelecs und E-Bikes erwartet.
Forciert wird zudem das Segment Batteriesysteme für Land- und Baumaschinen. Standorte unterhält Voltabox neben dem Headquarter in Delbrück unter anderem in Aachen, sowie in den USA und China. Mutterunternehmen ist die paragon GmbH & Co. KGaA.